20E – Alloy and Carbon Steel Bolting for Use in the Petroleum and Natural Gas Industries
With API Specification 20E, the American Petroleum Institute establishes manufacturing requirements for three (3) bolting specification levels: BSL-1, BSL-2, and BSL-3. These sequential bolting designations reflect increasingly stringent levels of technical performance, quality, and qualification criteria.
The product categories covered under API Specification 20E include:
a) machined studs
b) machined bolts, screws, and nuts
c) cold formed bolts, screws, and nuts (BSL-1 only)
d) hot formed bolts and screws <1.5 in. (38.1 mm) nominal diameter
e) hot formed bolts and screws 1.5 in. (38.1 mm) or greater nominal diameter
f) roll threaded studs, bolts, and screws <1.5 in. (38.1 mm) nominal diameter
g) roll threaded studs, bolts, and screws 1.5 in. (38.1 mm) or greater nominal diameter
h) hot formed nuts <.5 in. (38.1 mm) nominal diameter
i) hot formed nuts 1.5 in. (38.1 mm) or greater nominal diameter
Bolting Specification Levels for API 20E
The three bolting specifications provided by API 20E provide progressively rigorous bolting standards.
BSL-1 is the bolting specification level to which every fastener should conform. Manufacturing and coating processes are audited to ensure that specifications are met. Products are marked with the BSL-1 bolting specification level designation. Precise documentation, storage and shipping requirements are followed.
BSL-2 is the next bolting specification level, using non-destructive surface and ultrasonic testing to confirm bolt integrity.
BSL-3 is the most rigorous bolting specification level of API Specification 20E. BSL-3 prohibits continuous casting manufacturing and includes additional, increasingly rigorous testing requirements.
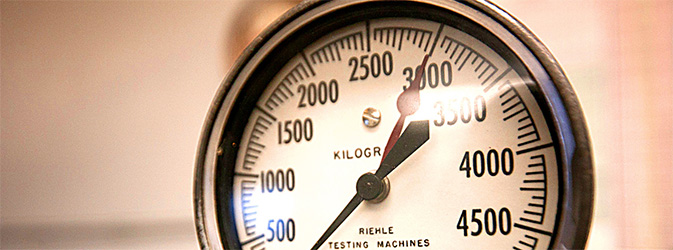
20F – Corrosion Resistant Bolting
API Specification 20F specifies requirements for the qualification, production, and documentation of corrosion-resistant bolting used in the petroleum and natural gas industries.
API Specification 20F covers the following product forms, processes, and sizes:
a) machined studs
b) machined bolts, screws, and nuts
c) cold formed bolts, screws, and nuts with cutor cold-formed threads
d) hot formed bolts and screws <1.5 in. (38.1 mm) nominal diameter
e) hot formed bolts and screws ≥1.5 in. (38.1 mm) nominal diameter
f) roll threaded studs, bolts, and screws <1.5 in. (38.1 mm) diameter
g) roll threaded studs, bolts, and screws ≥1.5 in. (38.1 mm) diameter
h) hot formed nuts <1.5 in. (38.1 mm) nominal diameter
i) hot formed nuts ≥1.5 in. (38.1 mm) nominal diameter
Bolting Specification Levels for API 20F
Two (2) bolting specification levels (BSL) are designated in API Specification 20F: BSL-2 and BSL-3.
These two BSL designations define increasingly higher levels of technical, quality, and qualification requirements: BSL-2 and BSL-3 are intended to be comparable to BSL-2 and BSL-3 as found in API 20E. The nominal BSL-1 is omitted from this standard.