On a recent tour of a switchgear assembly plant in the southeast, the tour guide called attention to a production line sitting idle in an otherwise bustling facility. “Supply chain issues,” she noted. “We’re waiting on a shipment of 8¢ screws, and it’s holding up $20,000 a day in production.”
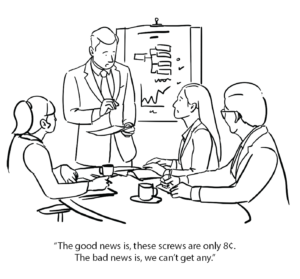
It was a glimpse into the challenges facing supply chain managers everywhere, as they work to source everything from computer chips for high-tech products, to low-cost screws and other components.
On this day at the switchgear plant, the lack of an 8¢ screw was a costly problem. Production was affected over multiple days, workers were idled, revenue was delayed, and backlogs were amplified.
This scene is familiar to companies who have experienced supply chain disruptions, as well as suppliers who have been negatively affected by upstream supply chains, material availability, and so on.
Avoiding domino effect disaster.
Ask any member of senior management if they have an interest in fasteners, and the answer will most likely be a polite no. But ask if they care about potential disruptions to the manufacturing capabilities of the enterprise, and watch their expression change.
It’s easy to take fasteners for granted, until there’s a problem. Even then, one might think that “finding a new supplier of screws will be easy”… or “we can import what we need from overseas”… or “I know of a fastener supply house in the next county.”
But of course, it’s not always that simple.
Creating reliable, long-term fastener solutions takes time. A single delay due to fastener out-of-stock can lead to hours, days, or weeks of lost productivity and missed deliveries.
This type of domino-effect disaster is to be avoided at all costs. When it comes to fasteners, failure is simply not an option. Managing the fastener supply chain for zero disruptions requires a commitment against the possibility of getting screwed.